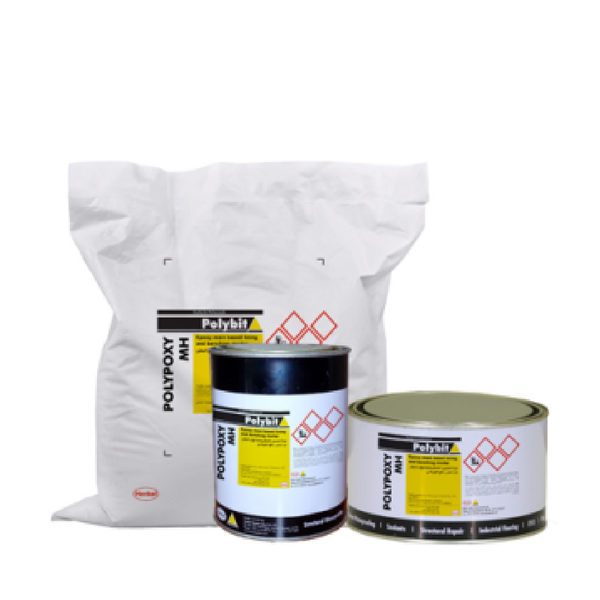
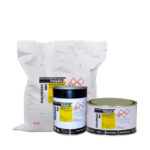
Polypoxy MH
Polypoxy MH
Epoxy resin based lining and benching mortar
Properties
- Highly resistant to a wide range of chemicals, acids and alkalis
- High impact and abrasion resistance
- Can be used in both dry and damp conditions
- Is thixotropic, hence can be applied vertically up to 10mm in a single application, a higher build up thickness may be applied in the second coat
- High humidity does not affect curing
- Shrinkage free hardening
- Increased water impermeability
- Odourless, can be used in enclosed applications
- Non-toxic, can be used in contact with potable water
- Easy to use – pre-weighed packs, requires only on site mixing
Description
Polypoxy MH is a three-component solvent free, thixotropic lining and benching mortar for protection of concrete. Polypoxy MH is based on a blend of epoxy resins and selected quartz aggregates. the cured render exhibits very high impact and chemical resistance.
TDS For Polypoxy MH
- Step by Step
Surface Preparation
The concrete surface should thoroughly be cleaned of all loosely adhering particles. Water jet blasting, sand or grit blasting is recommended for proper cleaning and removal of all deleterious materials. Traces of oil grease or curing compound is to be removed. Cracks and pot holes shall be repaired with a suitable repair mortar. water leakages if any are to be plugged with a quick setting mortar.
Priming
All surfaces shall be primed with Polyprime EP*(epoxy primer). the primer is to be properly applied on all the irregular surfaces on the concrete. On highly absorbent surfaces a second coat of primer is to be given. The epoxy render shall be applied when the primer coat is still tacky. Depending on the ambient temperature if the primer dries off fast, another coat shall be given prior to the application of the epoxy mortar. the pot life of the primer is about 30 minutes to 3 hours depending on the temperature. It is recommended to mix the primer for that area only on which it can be applied. the coverage rate is around 3-5 m2/l depending on the porosity of the substrate.
Mixing
Pour the entire contents of part B (hardener) into part a (base) and mix thoroughly for a few minutes with a paddle mixer fitted to a slow speed drill to get a homogenous mix. Then add the part C (powder) slowly into the mixed resins container and further mixed continuously till a uniform consistency is achieved. as the products are supplied in pre-weighed packs, part mixing is not at all recommended, since the cured product will not achieve its full properties even if there is a small variation in the mixing proportions.
Application
Apply the mixed mortar immediately after mixing on the tacky primed surface firmly with a steel trowel or spatula. For vertical and overhead surfaces the mortar is to be applied at a maximum thickness of 10mm to avoid sagging. However, for additional build ups, the epoxy mortar can be applied at thicknesses up to 30mm in the second layer. The second layer of application is to be done only after the first coat has achieved its initial cure i.e., after 24 hours of application. If a further layer is to be applied then the surface shall be cross hatched to get the mechanical key when the render is still wet. further priming is required if the second layer is to be applied after a period of 36 hours of application of the first layer.
Curing
The applied material will achieve its full properties after 7 days of application.