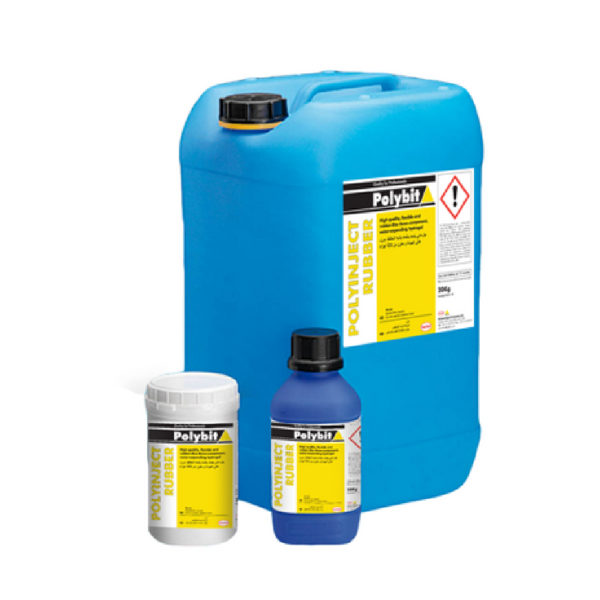
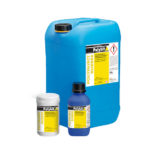
Polyinject RUBBER
Polyinject RUBBER
Three component low viscous acrylate gel injection grout for curtain wall, crack & expansion joint.
Properties
- Flexible
- Extreme low viscosity
- Can be used for injection hoses
Description
Polyinject Rubber is a three-component, waterexpanding hydrogel on acrylate or methacrylate basis that hardens to a rubber-like, flexible product. Polyinject Rubber can be applied in the case of grout curtains, brickwork injection, horizontal barriers, injection hose grouting and ground stabilization. Polyinject Rubber has an extremely low blending viscosity that is almost equivalent to the viscosity of water. This allows the use of Polyinject Rubber for injection applications for extreme fine cracks and massive walls with thicknesses above 50cm. In cured state Polyinject Rubber has a sound chemical resistance against many acids, bases, solvents and fuels etc. due to its high-quality material basis (see resistance list). During reaction and in a cured state Polyinject Rubber emits no toxic substances into the groundwater. product elements that are not built in during the reaction process (monomers, intermediates) are rapidly and completely biodegradable. differing pot lives can be defined (see table pot life), adapted to the application and environmental temperature, by varying the amount of b component (40 g to 1000 g based on 20 kg ai components).
TDS For Polyinject Rubber
- Step by Step
Surface preparation
The surface must be stable and free of separating substances. Insufficiently firm layers and concrete slurry must be removed. For this purpose the surface may be prepared by suitable mechanical processes such as e.g. shot blasting, milling or any other suitable mechanical means. Blow the cracks and treated surface with oil free air to ensure complete removal of all dust and loose particles. In the presence of running water the flow must be stopped using Polyinject Stop which produces a rapid setting water-stopping foam. when the water is stopped the cracks are re-injected with Polyinject Rubber
Work preparation
POLYINJECT RUBBER is be applied as injection resin using injection packers and 2-c pumps equipped with a flushing unit. The injection packers may be fixed into holes drilled directly into the crack or drilled diagonally from concrete adjacent to the crack or by the fixing of injection nipples. For further assistance and instructions regarding the packer fixing and design please refer to our method Statement.
Mixing
Polyinject Rubber consists of 3 components. The AII container is poured completely into the AI container and mixed for approx. 3 minutes. The B component is filled in the desired amount into a container equivalent to the AI component and filled with clean tap water up to the same mass as AI + AII, then it is mixed again for 3 minutes. the A and B components prepared in this way are ready for use and are processed 1 : 1 with a 2-component injection pump equipped with a flushing unit. The use of the injection pumps that feature forced conveyance of 1 : 1 (a to b component) is recommended in order to prevent mixing errors. The AI component activated with aii can be used for approx. 24 hours (depending on temperature). Using the activated ai component is not recommended after this period. the ready-for-use B component remains stable for approx. 5 hours (depending on temperature). e required potlife can be defined depending on the amount of b component (salt) and the temperature. The amount of component B should never be below 40 g (based on 20 kg of al component) to assure a reliable reaction. Likewise should the amount component B not exceed 1000 g (based on 20 kg of al component) to avoid degradation of the product properties. The amount of component B shall never exceed 300 g (based on 20 kg of AI component) in case of crack injection on reinforced concrete. Never mix the ai+aii mixture together with b component.
Injection
Polyinject Rubber can be injected with a 2-component injection pump equipped with a flushing unit.