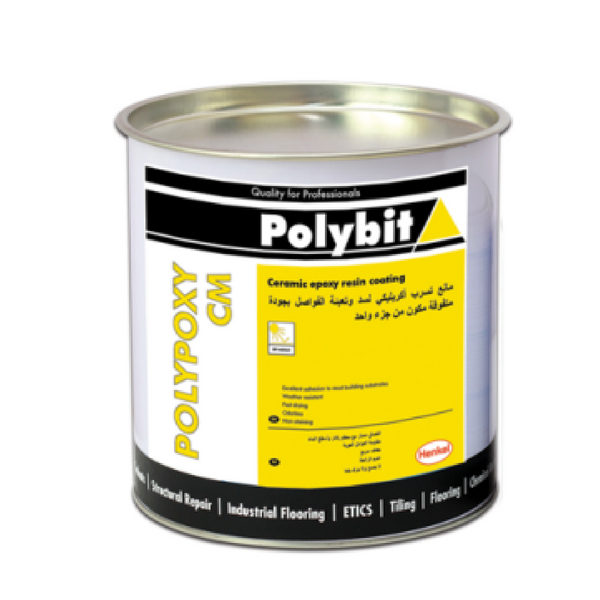
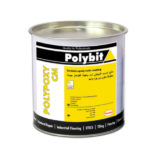
Polypoxy CM
Polypoxy CM
Ceramic epoxy resin coating
Properties
- Excellent resistance to a wide range of chemicals & solvents
- Excellent water immersion properties.
- Excellent resistance to high temperature cathodic disbanding.
- Excellent adhesion, abrasion and wear resistance.
- Durable, self priming, high build with smooth sprayable consistency.
- Solvent free – No VOC’s
- Good sag resistance
Description
Polypoxy CM is a versatile two component solvent free ceramic epoxy resin coating , it is designed to protect metal surface against abrasive and corrosive agents, it provide a durable and impervious coating which has excellent water immersion properties and have excellent resistance to a wide range of chemicals.
TDS For Polypoxy CM
- Step by Step
Surface Preparation
Surface preparation for concrete : Surface preparation plays a vital role in determining the durability of any floor coating. therefore proper care should be taken while executing it. The surface should be dry, free of any cement laitance, oil and grease, curing compound and any other contaminants, which may affect the bonding. Light mechanical scabbling, grit/captive blasting or grinding is recommended for cleaning the surface of such contaminants. new concrete surfaces should be 28 days old and the moisture content on the surface must be less than 5%. Refurbishment of existing or old floors must be done with a suitable repair mortar, in order to ensure that the bond between the old substrate and the new flooring system is very good. Surface irregularities and blow holes shall be repaired with Polypoxy EP* (epoxy resin based blow hole filler and skimming mortar) or Ceresit RS 88* (cementitious repair mortar). Alternatively an epoxy resin based scratch coat can be used when repairing larger areas (>0.5m2). The surface after carrying out the necessary cleaning shall be vacuumed for removing the dust debris left over after the cleaning process. Ensure that the moisture content in the substrate is below 5%.
Surface preparation for steel : The performance of a coating is significantly influenced by its ability to adhere properly to the substrate material. Residual millscale on steel surfaces is an unsatisfactory base to apply modern, high performance protective coatings and is therefore removed by abrasive blast cleaning. Other surface contaminants on the rolled steel surface, such as oil and grease are also undesirable and must be removed before the blast cleaning process.
Primer
On most new concrete floors priming may not be required. However for best adhesion, prime the prepared surface with Polyprime EP* @ 4-5m2/lt. The coating is applied when the primer is in a tacky to semi-tacky condition. However, in all circumstances, the coating shall be applied within 12 hours of application of the primer. If the primer surface is left open for more than 12 hours, then a fresh coat of primer has to be re-applied. on a steel substrate the first coat should be applied immediately after cleaning to prevent rusting or contamination.
Mixing
Mix part A (resin) and part B (hardener) separately for 1 minute using a slow speed drill fitted with a paddle. Then add part B into part A and mix thoroughly for 2 – 3 minutes to achieve uniform consistency. Apply immediately after mixing. Part mixing is not recommended since the components are supplied in premixed kits. Mixing Ratio, by volume- Resin: Hardener is 2:1
Application
Bulk Spray System
– two component abrasion resistant airless equipments with a minimum compression ratio of 60:1.
– nozzle 3 to 4 mm.
– fan width 50 to 60°C, depending on the structure to be coated.
– Spraying pressure: 210 bar minimum.
– product temperature: ≥25°C.
for cartridge system:
– pre-heat cartridges to 50°C.
– Set product pressure to approximately 2 bar and air pressure to approximately 5 bar.
Film thickness per coat: 200 to 300 microns. Ambient and substrate temperature range: 15 to 40°C. Relative humidity: <85 %; substrate temperature must always be 3°C higher than the dew point. If application is interrupted the spray gun should be flushed within 5 minutes with a suitable cleaner, from the flushing pump. Multiple coat application may be carried out, once the film has gelled, but not cured beyond the maximum recoat time. If this time has elapsed, light abrasive blasting is required, followed by a solvent wash to remove any abrasive residues. Brush & roller applications are recommended for sport repair and stripe coating.
Curing
At least four days of curing is recommended with ventilation at temperature above 25°C, longer curing time is required if temperature is lower than 25°C.