
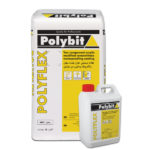
Polyflex
Polyflex
Two part acrylic modified cementitious waterproofing coating
Properties
- Good flexibility. Thermal co-efficient of expansion similar to that of concrete
- Good adhesion to both, porous and non porous surfaces
- Good mechanical properties
- Suitable for light pedestrian traffic
- Excellent durability to long term weathering effect and UV
- Non toxic, therefore suitable for use in potable water applications
- Resistant to carbon dioxide and chloride ion diffusion
Description
Polyflex is a two part acrylic modified cementitious coating for protecting concrete structures against water, vapor, ingress of chloride ions, attacks of acidic gases and alkalis. It cures to form a tough flexible coating having excellent waterproofing properties. Polyflex is a blend of cement, selected fillers, polymers and graded silica sand which is in the powder form. The liquid contains acrylic co-polymers and wetting agents.
TDS for Polyflex
- Step by Step
Step by Step
Substrate Preparation
The surface must be structurally sound and free of oil, grease, dust and other contaminants which will affect the bonding. Any structural cracks and potholes shall be repaired with a suitable repair mortar from the Polycrete* range of repair mortars. The surface to be treated should be presaturated with water prior to application. However, any standing water shall be removed prior to application.
Mixing
Polyflex is supplied in two pre-measured parts which just requires on site mixing. Do not mix more material than that can be used within the pot life. Part mixing can be carried out by mixing 3 parts of powder with 1 part of liquid (by weight). Pour the liquid into a suitable container and slowly add the powder to the liquid. Mix the contents using a slow speed drill (300-400rpm) fitted to a proprietary paddle mixer till a homogenous, lump free and creamy consistency is achieved. DO NOT ADD WATER TO DILUTE THE MATERIAL.
Application
It is recommended to apply Polyflex in two coats to provide a minimum thickness of 2mm for heavily trafficked areas and water retaining structures. Each coat shall be applied @1.8 kg/m2 which will give a dry film thickness of 1mm. The coating can be applied with a stiff brush or by an airless spray of nozzle size of 3-4mm and a pressure of 6-7 bar. After the application of the first coat and whilst the coating is still wet, embed a glass fibre mesh at all corners and other joints for added reinforcement. The second coat shall be applied after the first coat dries off completely (6-8 hours @25°C, 50% RH). For general waterproofing and protection against carbonation and alkali attacks, the coating can be applied in 1mm thickness.
Protection
Adequate protection needs to be provided for the coating in the following conditions: areas subjected to mechanical abrasion flowing water areas